



Non-Toxic, OEM Compliant Metal Protection
A Surface-Active, Metal Passivation Technology
For Low, Medium & High Pressure Boilers
Control Your Lifetime
Corrosion Protection
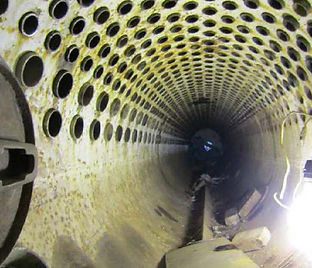
Before
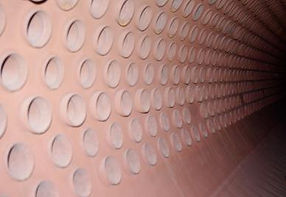


After Using Anodamine
1 Week
1 Year
An innovative water treatment
Company delivering the only
Non-toxic, OEM – compliant metal
Protection product that actually
Benefits Of Anodamine
Reduce corrosion Product Transport
Eliminate Flow-Assisted Corrosion
Improve Reliability & Availability
Layup Protection ( Short & long term wet or dry )
Reduced Frequency or Eliminate Chemical Cleans
Production from Corrosion Fatigue/Stress Corrosion Crcking
Saveing in Fuel. Water, and Emissions

Key Performance Indicators
Non-toxic and environmentally friendly
Anodamine HPFG and the entire range of Anodamine chemical products are non-toxic and environmentally friendly, with the only exception of custom blends using neutralizing amines required by a customer’s selection. With an LD50 rating of 169,600 mg/kg, Anodamine HPFG is the only truly non-toxic option on the market.
Thermally stable
Anodamine products are highly resilient to thermal degradation and are field-tested with no degradation products up to 4500 psi / 310 bar and 1051°F / 566°C on many high-pressure boilers, ranging from subcritical drum units through to supercritical once-through generators, which deliver an operational CACE of approximately 0.08 uS/cm while maintaining a routine dosage of 1 ppm Anodamine proportional to feedwater flow.
No increase in circuit pH or standard conductivities
Traditional film-forming amines (FFAs) and products available on the market are typically not water-soluble and therefore use neutralizing amine/alkalizing amine products to ensure their solubility and stability in form of supply. Anodamine’s specialized chemical formulations are fully water-soluble, emulsion-free, and do not use any neutralizing or alkalizing amine products. With Anodamine, there is no risk of overdosing and/or creating gunk balls in a system.
Prevents pitting and the propagation of stress corrosion cracking (SCC)
Anodamine has been shown to slow and even eliminate SCC-related failures by its unique isolation of the anode from the corrosive environment. Anodamine is able to selectively penetrate the oxides and reach the virgin base metal, a characteristic exclusive to the Anodamine technology, which achieves specialized hydrophobic isolation of the virgin metal, ultimately preventing the corrosive attack and eliminating the threat of pitting as a source for the propagation of SCC.
No overdosing risks
Overdosage happens. It is a reality that sometimes cannot be avoided. Anodamine understands this, which is why Anodamine products are void of any limitations regarding overdosage. Where other products will cause numerous consequences with overdosage, such as steam drum foaming/carry-over, increased boiler blowdown, reduced heat transfer efficiency/increased fired fuel, and increased environmental discharge (to name a few), should any overdosage occur while utilizing Anodamine, there are no risks to the user, the plant, or the environment.
Single and two-phase flow-accelerated corrosion (FAC) protection
Anodamine possesses a unique volatile to liquid partition ratio that enables the product to remain in both the liquid and vapor phases of a cycle at temperature. This presence in both the liquid and vapor provides protection against not only single-phase FAC, but also two-phase FAC, an extremely damaging form of FAC which other products simply cannot address.
Mitigation of oxide transport
Conventional film-forming amines (FFAs) and products available on the market use neutralizing and alkalizing amines as part of their product mixture. These neutralizing/alkalizing amines break down in the cycle and produce organic acids, which are shown to complex, destabilize, and transport iron. These breakdown products/acids also affect the FFA product itself, resulting in gunk balls, fatty deposits, and fouling. Through isolation of the anode and being a single-substance product, Anodamine provides protection and stability to the base metal and the oxides, mitigating oxide transport problems and allowing a clean, rapid, and reliable return-to-service after layup
No waxy “ gunk” balls
Anodamine does not change the cycle pH and has no appreciable effect on measured conductivities. With Anodamine, ammonium hydroxide is the recommended alkalization and pH-buffering additive. In comparison, conventional film-forming amines and competitive products are required to use neutralizing amines for solubility issues, resulting in a multi-component mixture that unnecessarily creates an extreme limitation between pH control and metal protection.
No negative effects on online instrumentation
The measurement and monitoring of a system’s chemistry-related parameters is crucial. Online instrumentation and equipment used for these key measurements are unaffected by Anodamine dosage. Anodamine does not blindly form coatings on all surfaces, like other products. The Anodamine technology is specifically engineered to selectively target virgin metal and heat exchange surfaces (where the corrosion occurs).
Protection of all-ferrous and mixed metallurgy systems
The Anodamine protection mechanism works for both ferrous and mixed metallurgy systems since Anodamine’s isolation of the anode extends to both ferrous and copper-based alloys. Since Anodamine’s unique approach to metal protection selectively isolates the virgin base metal from the cooling medium, mixed metallurgy systems can successfully operate under AVT(O) treatment regimes, making the use of oxygen scavengers and reducing agents obsolete. Alloys remain protected independent of oxygen residual, ammonia dosage, load changes, or cycle air-in-leakage.
Full OEM compliance
There are a number of international standards that exist for steam-water cycle chemistry controls. Additionally, there are turbine OEM guidelines for steam quality compliance to turbines. The Anodamine products are thermally stable and offer full compliance with all international steam-water cycle chemistry guidelines and turbine OEM guidelines. Anodamine is successfully applied in many high-pressure boilers, ranging from natural and forced circulation, subcritical drum units, all ferrous and mixed metallurgy units, HRSG and cogeneration configurations with air-cooled and/or evaporative condensers, through to supercritical once-through generators, which deliver an operational CACE of approximately 0.08 uS/cm while maintaining a dosage of 1 ppm Anodamine proportional to feedwater flow and an active Anodamine residual of 800-1000 ppb.


•1 x 2,600 psi / 179 bar, CE Natural circulation, mixed metallurgy drum units with 475 MW WH Turbines, commissioned in 1964. HP steam is reheated to 1,050 oF / 566 oC.
•1 x 1,935 psi / 133 bar, B&W Natural circulation, mixed metallurgy drum units with 125 MW GE Turbines, commissioned in 1958. HP steam is reheated to 1,050 oF / 566 oC. (retired)
•Unit 1 is retired, Unit 2 was converted from AVT(R) – Hydrazine / CT to Anodamine / AVT(O) / CT in 2013.
•Unit 2 is a peaking unit operating anywhere from 2 to 20 hours per start-up.
•The unit operates at 10 to 15% of available time.